Vorausschauende Instandhaltung : Die 5 Schritte von Predictive Maintenance
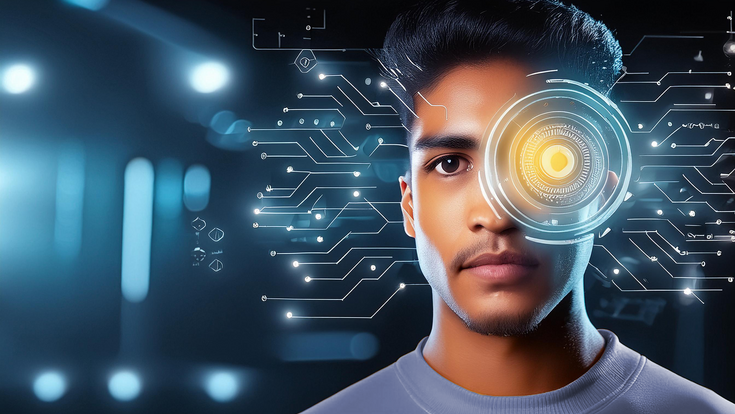
Predictive Maintenance, auch vorausschauende Wartung oder Instandhaltung genannt, ist eine Methode, um den Wartungsbedarf von Maschinen vorherzusagen. Dazu werden per Echtzeitüberwachung Betriebsdaten erfasst und unter Einbeziehung weiterer Informationen von intelligenten Algorithmen ausgewertet. Durch Anomalieerkennung können Verschleiß sowie drohende Ausfälle frühzeitig identifiziert und Wartungsarbeiten vorausgeplant werden, noch bevor es zu Problemen kommt.
Instandhaltungsstrategien im Vergleich
Die vorausschauende Instandhaltung ist ein proaktiver Ansatz, der darauf abzielt, Wartungen und Reparaturen so früh wie möglich durchzuführen – aber auch nur dann, wenn sie wirklich nötig sind. In dieser Hinsicht unterscheidet sich Predictive Maintenance von anderen Instandhaltungsarten:
• Reaktive Instandhaltung
Wartungen und Reparaturen werden erst durchgeführt, wenn Fehler auftreten oder der Verschleiß bereits weit fortgeschritten ist.
• Präventive Instandhaltung
In regelmäßigen Abständen werden Inspektionen und Wartungsarbeiten durchgeführt, unabhängig vom tatsächlichen Zustand der Anlage.
• Zustandsorientierte Instandhaltung
Die zustandsorientierte Wartung erfolgt ebenfalls reaktiv, allerdings auf Basis von Maschinendaten. Instandhaltungsarbeiten werden durchgeführt, sobald bestimmte Schwellenwerte erreicht sind.
Die 5 Schritte der vorausschauenden Instandhaltung
Predictive Maintenance ermöglicht es, datenbasierte Vorhersagen über den Zustand einer Anlage zu treffen und Instandhaltungsmaßnahmen entsprechend zu planen. Aber woher stammen die Informationen? Wie lässt sich der optimale Zeitpunkt für Wartungsarbeiten ermitteln? Und welche technischen Voraussetzungen sind dafür nötig?
Schritt 1: Datenerhebung
Im ersten Schritt werden Betriebsdaten mithilfe von Sensoren an den Maschinen erfasst und per IoT-verbindung in einer Datenbank gespeichert. Bei SSI Schäfer wird dafür die „Nano Box“ genutzt, ein Standard IPC von Siemens, um die Echtzeitdaten auf Steuerungsebene abzugreifen und anschließend in das Computerized Maintenance Management System, das WAMAS Maintenance Center, zu übertragen.
Schritt 2: Datenanalyse
Die gesammelten Daten werden dann mit weiteren relevanten Informationen zusammengeführt. Stichwort: Big Data. Neben der individuellen Wartungshistorie, die über das WAMAS Maintenance Center zur Verfügung steht, werden bei SSI Schäfer auch globale Maschinendaten herangezogen. Auf dieser Basis können spezielle Datenanalyse-Algorithmen und Machine-Learning-Technologien Muster und Anomalien erkennen.
Schritt 3: Vorausschauende Diagnose
Durch statistische Verfahren und Modellierungen werden aus den Analyseergebnissen vorausschauende Diagnosen über den zukünftigen Zustand von Maschinen und Komponenten erstellt. Auch hier kommt künstliche Intelligenz zum Einsatz. Anhand neuer Daten lernt das System ständig dazu und liefert immer präzisere Vorhersagen.
Schritt 4: Wartungsplanung
Die erstellten Prognosen geben Aufschluss über den idealen Zeitpunkt und die Art der erforderlichen Wartungsarbeiten. Diese lassen sich dadurch vorausschauend planen, sodass Ersatzteile rechtzeitig bestellt und Maschinenausfälle vermieden werden können.
Schritt 5: Durchführung der Wartung
Die Instandhaltungsmaßnahmen können auf Basis der vorangegangenen Planung besonders effizient durchgeführt werden – etwa zu Schwachlastzeiten sowie mit bedarfsgerechtem Material- und Personalaufwand.
Predictive Maintenance erhöht nicht nur die Verfügbarkeit, sondern trägt auch dazu bei, die Lebensdauer von Maschinen und Anlagen zu verlängern. Mithilfe von Datenanalysen werden Probleme schon im Anfangsstadium erkannt, bevor größere Schäden entstehen. Auch Verschleiß kann durch eine bedarfsorientierte Wartung minimiert werden. Langfristige Investitionen werden somit geschützt und die Nachhaltigkeit der Anlage verbessert.
Herausforderungen von vorausschauender Instandhaltung
Die erfolgreiche Implementierung von Predictive Maintenance bringt einige Herausforderungen mit sich. Neben dem Aufbau der nötigen Infrastruktur zur Kommunikation der Systeme bedarf vor allem die Auswahl und Anwendung geeigneter Analyseplattformen und KI-Modelle ein besonderes Know-how. Auch die Qualität der Daten ist von entscheidender Bedeutung – mangelnde Informationen können zu ungenauen Vorhersagen und falschen Wartungsentscheidungen führen.