Case Study : Würth setzt auf Automatisierungs-Lösung von Knapp
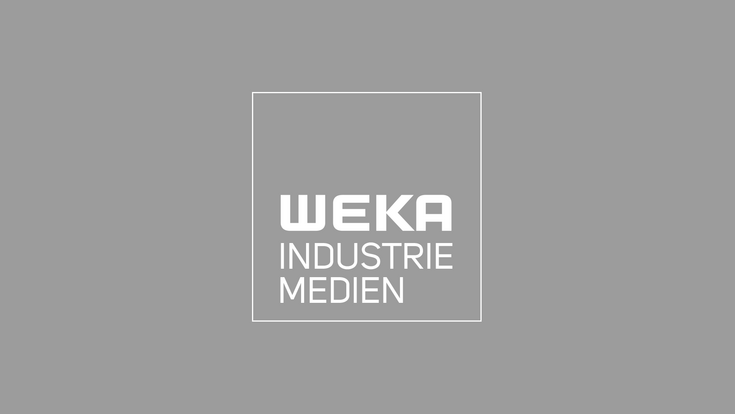
„Wir mussten in Böheimkirchen ganz einfach einen neuen Schritt gehen, die Ressourcen haben nicht mehr ausgereicht.“ Stefan Gugerell, Geschäftsführer Logistik bei Würth Österreich, stand vor dem Problem, das wirtschaftlicher Erfolg oft mit sich bringt. Das Würth-Logistikzentrum in Böheimkirchen, von dem aus die über ganz Österreich verteilten Shops beliefert werden, war an seine Grenzen gestoßen, die Lagerressourcen ausgeschöpft, das Anlagenkonzept nicht mehr effizient genug.
Um Produktivität und Serviceleistung aufrechtzuerhalten, war ein Zubau notwendig, und die neue Lösung entstand gemeinsam mit dem langjährigen Partner Knapp. Eine Lösung, die den gesamten intralogistischen Prozess umfasst.
Bereits im Decanting-Bereich kommt das OSR Shuttle Evo zum Einsatz: Die gelieferten Artikel werden vereinzelt und in Würth-Lagerbehälter umgepackt. Danach machen sich die Behälter auf den Weg Richtung OSR Shuttle Evo, wo sie bis zur Kommissionierung zwischengelagert werden. Sobald ein Kundenauftrag ansteht, werden die Versandkartons mithilfe von vollautomatischen Kartonaufrichtern produziert. Je nach Auftragsgröße stellen die Maschinen Kartons in zwei unterschiedlichen Größen zur Verfügung.
Für die Würth-interne Belieferung werden die Artikel in Mehrwegbehälter kommissioniert. Diese werden beim Auftragsstart automatisch aufgeklappt und dem System bereitgestellt. Um eine eindeutige Zuordnung zum Kunden und zum Auftrag zu garantieren, erhält jeder Karton oder Behälter ein Routinglabel. Dieses Label ist nicht nur für den Transport durch das Lager notwendig, sondern triggert auch alle anderen Prozesse im Lager an.
Drei Gassen, 41 Ebenen, 57.000 Stellplätze
Bei der Kommissionierung arbeiten das OSR Shuttle Evo und der Pick-it-Easy Evo-Arbeitsplatz Hand in Hand. Das OSR Shuttle Evo versorgt die angeschlossenen Pick-it-Easy-Arbeitsplätze just-in-time mit Waren. Jeder Arbeitsplatz hat dabei Zugriff auf jeden Artikel im System. Das flexible Regalsystem und das schlanke Design ermöglichen eine optimale Platzausnutzung. Das OSR Shuttle Evo ist auf zukünftige Erweiterung ausgerichtet: Die Anzahl der Shuttles und der Lifte ist skalierbar, wodurch die Leistung an die jeweiligen Anforderungen angepasst werden kann.
Das Shuttle-System bietet mit drei Gassen und 41 Ebenen Stellplätze für rund 57.000 Kartons und Behälter. Neben den Lagerbehältern für die Kommissionierung werden auch fertiggestellte Versandkartons bis zum Versand in den Regalen zwischengelagert. Über 100 Shuttles bringen die Behälter und Kartons immer dorthin, wo sie gerade benötigt werden – das OSR Shuttle Evo versorgt dabei sowohl die angeschlossenen Pick-it-Easy Evo-Arbeitsplätze als auch die Versandroboter flexibel und in der richtigen Reihenfolge.
Anhand der Auftragsdaten schickt die Knapp-Software KiSoft die Behälter und Kartons in der richtigen Reihenfolge Richtung Kommissionierung oder Versand. Der Versand durch die unterschiedlichen Lagerbereiche erfolgt dabei über die Knapp-Fördertechnik Streamline.
„Möglichst abwechslungsreiche Arbeit“
Die Zusammenstellung der Kundenaufträge erfolgt an sechs Pick-it-Easy Evo-Arbeitsplätzen. „Wir wollen die Arbeit möglichst abwechslungsreich gestalten“, sagt Stefan Gugerell, „und daher setzen wir in der Logistik immer mehr auf Job-Rotation. Dafür ist es aber zwingend notwendig, eine Software einzusetzen, die die Mitarbeiter unterstützt, um auch die Einschulungszeiten so gering wie möglich zu halten.“ Die neuen Arbeitsplätze unterstützen und motivieren Mitarbeiter in ihrer täglichen Arbeit und schaffen so ein neues Arbeitserlebnis. LED-Anzeigen und Touchscreens mit intuitiven easyUse-Benutzeroberflächen und Add-ons zur Qualitätssicherung schaffen eine spezielle User Experience. Auch individuelle Anpassungen an die Kundenprozesse sind in die Konzeption der Arbeitsplätze miteingeflossen.
Die Versorgung der Arbeitsplätze erfolgt über das OSR Shuttle Evo im Ware-zur-Person Prinzip – die Mitarbeiter bekommen automatisch zur richtigen Zeit und in der richtigen Reihenfolge die Waren an den Arbeitsplatz zur Verfügung gestellt. Das verringert Wegzeiten und führt zu einer deutlichen Steigerung der Produktivität und Kommissionier-Qualität. Die Mitarbeiter arbeiten an den Pick-it-Easy Evo-Arbeitsplätzen intuitiv und fehlerfrei. Das ermöglicht größtmögliche Leistung bei geringem Kraftaufwand.
Ivii sorgt für Sicherheit
Fertige Kundenaufträge durchlaufen vor dem Versand mehrere Stationen zur Qualitätskontrolle. Jeder fertiggestellte Karton durchläuft auf dem Weg Richtung automatische Deckelung die ivii.photostation. Diese erstellt mithilfe von modernster Bilderkennungstechnologie ein Bild des Kartoninhalts und sieht auf einen Blick, ob die Artikel im Karton sicher verstaut sind. Falls dies nicht der Fall ist, schleust das System die Kundenaufträge automatisch aus und bringt sie zu einer Kontrollstation. Dort gibt ein Mitarbeiter zur Sicherung des Inhalts Füllmaterial aus 100 Prozent biologisch abbaubarem Material bei, wodurch die Artikel sicher und unversehrt beim Kunden ankommen. Das erstellte Bild ermöglicht zudem eine einfache Rückverfolgung.
Auf dem Weg zur fehlerfreien Lieferung spielt auch ein Open Shuttle eine zentrale Rolle. Kartons, die bei der Wiegekontrolle Abweichungen zeigen, werden für eine weitere Überprüfung an einen Kontrollarbeitsplatz gebracht. Damit die Mitarbeiter körperlich entlastet und Wegzeiten reduziert werden, übernimmt ein Open Shuttle den Transport der zu kontrollierenden Kartons von der Versandlinie zum Kontrollarbeitsplatz.
Der freifahrende Roboter erledigt seine Arbeit dabei völlig autonom und ohne optische oder physische Hilfsmittel. Dank der Navigationstechnik, die auf natürlicher Konturenerkennung basiert, planen sie selbstständig ihren Weg und weichen Hindernissen aus.
Automatisches Falten und Deckeln
Nach der Qualitätskontrolle machen sich die Versandkartons fertig für die Palettierung und Auslieferung. Nach der automatischen Lieferscheinbeigabe fahren die Kartons in Richtung der vollautomatischen Falt- und Deckelungsmaschinen. In der Faltmaschine werden die Höhe des Inhalts kontrolliert und der Karton mithilfe des Faltmechanismus auf die minimale Höhe reduziert. Diese Reduktion der Kartongröße bringt eine wesentliche Platzeinsparung auf der Palette und in weiterer Folge im Lkw mit sich.
Nach der Faltung erfolgt die vollautomatische Deckelung. Nach der Anbringung des Versand- und der Gefahrenlabels ist der Karton bereits für die Auslieferung zum Kunden. Je nach Versandplanung fährt der fertiggestellte Versandkarton zurück ins OSR Shuttle Evo, wo er bis zum Versand zwischengelagert wird. Steht die Auslieferung für die jeweiligen Aufträge gleich an, transportiert die Fördertechnik die Kartons direkt zum vollautomatischen Versandroboter.
Versandroboter entlasten den Menschen
Zur Entlastung der Mitarbeiter kommen in der neuen Lösung auch zwei Versandroboter zum Einsatz. Die Knickarmroboter übernehmen die Palettierung der Kartons und Mehrwegbehälter vollautomatisch und befreien somit die Mitarbeiter von dieser körperlich belastenden Tätigkeit. Jeder Roboter hat gleichzeitig Zugriff auf acht Versandpaletten. Diese befüllt er platzsparend und in der richtigen Reihenfolge. Bis zu 7.000 Pakete pro Stunde finden so ihren Weg auf die Versandpaletten, die an Kunden in ganz Österreich zugestellt werden.
Grüne Schritte
Das Würth-Logistikzentrum in Böheimkirchen setzt auch Standards in Sachen Nachhaltigkeit.
Ein zentraler Aspekt bei der Modernisierung der Logistik war die Reduktion der Umweltbelastung. Die Energiegewinnung am Standort erfolgt zukünftig mithilfe der derzeit größten Eigenverbrauchs-Photovoltaikanlage Niederösterreichs. Und der Ansatz spiegelt sich auch in der Intralogistik:
– Zwei vollautomatische Versandroboter übernehmen die Palettierung der Kartons und Mehrwegbehälter für den Versand. Die Kartons werden dabei möglichst platzsparend auf die Palette geschlichtet, damit die Anzahl der Versandpaletten so gering wie möglich gehalten wird.
– An vollautomatischen Falt- und Deckelungsmaschinen für Kartons werden die Versandkartons mittels individueller Faltung soweit wie möglich in ihrer Höhe reduziert. Dadurch kann das Transportvolumen um rund 20 Prozent reduziert werden, wodurch bis zu vier Lkw-Fahrten pro Tag eingespart werden.
– Mittels innovativer Bilderkennungstechnologie der ivii gmbh – des Spezialisten für Bildverarbeitung innerhalb der Knapp-Gruppe – wird das Schlichtmuster im Versandkarton kontrolliert, um Freiräume im Karton zu erkennen. Diese werden gegebenenfalls mit einer zu 100 Prozent biologisch abbaubaren Folie aus Mais- und Kartoffelstärke befüllt. Das reduziert Beschädigung und Bruch von Artikeln, wodurch die Umweltbelastung durch Rücksendungen und Doppellieferungen vermieden wird.
– Die Lieferung der Artikel an Würth-interne Kunden erfolgt in Mehrwegbehältern. Die Lösung ist so konzipiert, dass sowohl Kartons als auch Mehrwegbehälter mit den eingesetzten Technologien bearbeitet werden können.
Auftraggeber
Die Produktpalette von Würth Österreich (Böheimkirchen) umfasst über 125.000 Artikel von Montage- und Befestigungsmaterial über Werkzeuge bis zu chemisch-technischen Produkten und Arbeitsschutz. Das Unternehmen wurde als zweite Würth-Auslandsgesellschaft 1962 in Wien gegründet und beliefert aktuell rund 55.000 Kunden. 1999 wurde der Firmensitz nach Böheimkirchen, verlegt. Würth Österreich beschäftigt rund 900 Mitarbeiter und erwirtschaftete im Geschäftsjahr 2019 einen Umsatz von 220 Millionen Euro.
Auftragnehmer
Knapp (Hart bei Graz) zählt zu den Markt- und Technologieführern unter den Anbietern intralogistischer Komplettlösungen, automatisierter Lagersysteme und Lagerlogistik-Software. Weltweit vertrauen zahlreiche Kunden aus den Branchen Healthcare, Retail, Fashion, Food Retail und Industry auf die Erfahrung und Innovationskraft der Knapp-Gruppe. Das Unternehmen beschäftigt an weltweit 43 Standorten mehr als 4.500 Mitarbeiter, 2.900 davon allein in Österreich. Im Jahr 2018/19 verzeichnete Knapp einen Auftragseingang von 1,25 Milliarden Euro.