Case Study : So optimiert Airbus seine Intralogistik
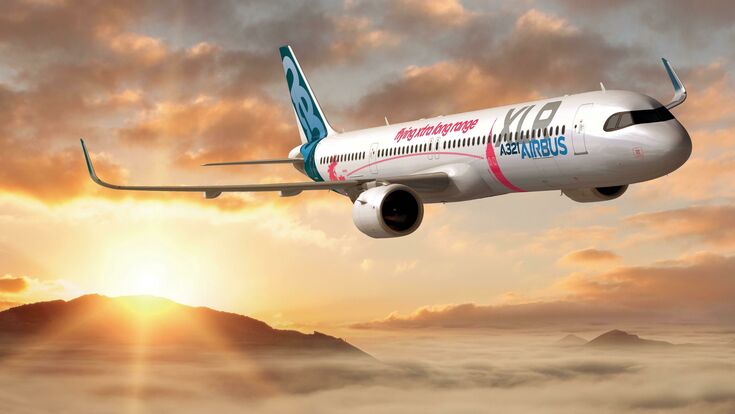
Für das neue Langstreckenflugzeug A321 XLR hat Airbus am Standort Hamburg-Finkenwerder eine eigene Ausrüstungsmontagehalle errichtet. In dem 38 Meter hohen neuen XLR-Hangar erfolgt parallel die Ausrüstungsmontage von mehreren A321 XLR-Flugzeugrümpfen. Zur Prozessoptimierung setzt Airbus auf eine maßgeschneiderte montrac-Intralogistikanlage für eine umfangreiche und individualisierte Automatisierung des Materialflusses vom Lager (Sequencer) zu den einzelnen Arbeitsstationen.
Die eigens für Airbus entwickelten montrac-Shuttles transportieren dabei autonom gesteuert Kleinladungsträger auf einer rund einen Kilometer langen verzweigten Monoschienenstrecke. Diese verbindet den Sequencer mit zwei Montagebühnen, an die 13 doppelstöckige Arbeitsstationen angeschlossen sind. Für eine optimale Raumnutzung verläuft zudem ein Teil der Monoschienentransportstrecke unterirdisch durch einen Tunnel, in dem das montrac-System unter der Decke montiert ist.
Jede Arbeitsstation besteht aus zwei Decks mit wiederum jeweils vier Zugriffsebenen, aufgeteilt in Elektrik, Mechanik, Hydraulik und Leergutrückführung, die von den Shuttles je nach Bedarf autonom angesteuert werden. Die Beladung der montrac-Shuttles mit Kleinladungsträgern am Sequencer, der Transport zu den Montagebühnen und Arbeitsstationen sowie die bedarfsgerechte Anlieferung an die jeweiligen Zugriffsebenen sowie die Rückführung der leeren Kleinladungsträger laufen voll automatisiert ab.
Dabei erfolgt der Vertikaltransport der Shuttles zu den Montagebühnen, Arbeitsstationen, Decks und Zugriffsebenen sowie die Rückführung des Leerguts über zahlreiche montrac-Lifte. Somit ist eine manuelle Tätigkeit lediglich bei der Entnahme der Kleinladungsträger und Leergutrückgabe an den Arbeitsstationen sowie für die Leergutrückführung am Sequencer (Kompaktlager) notwendig.
Aufgrund der intelligenten Hightech-Steuerung kennt jedes Transportshuttle genau seine Position und sein Transportziel und bringt so die richtigen Kleinladungsträger zur richtigen Zeit an die richtige Zugriffsebene bzw. zurück zum Sequencer. Fällt ein Shuttle aus, kann es jederzeit individuell mit einem Handgriff aus dem laufenden System entfernt oder ausgetauscht werden, ohne dafür die Anlage zu stoppen. Dank der intelligenten Steuerung kennt auch ein ausgetauschtes Transportshuttle sofort das ursprüngliche Transportziel.
„Besonders bedeutend für Airbus war neben dem geringen Platzbedarf und der Zuverlässigkeit des montrac-Systems vor allem die hohe Energieeffizienz aufgrund des minimalen Stromverbrauchs. Im Vergleich zu anderen Systemen, die meist dauerhaft laufen, benötigen die Niederspannungsantriebe der montrac-Shuttles nur während der Fahrt Strom und hinterlassen einen minimalen CO2-Fußabdruck. Dadurch ergibt sich ein signifikantes Energieeinsparungspotential“, betont Worm.
Das nach dem Baukastenprinzip aufgebaute Transfersystem montrac besteht aus einem modularen Aluminium-Monoschienensystem mit integrierter Stromschiene, auf dem die speziell für Airbus entwickelten montrac Shuttles autonom gesteuert operieren und eigenständig die optimale Route zum jeweiligen Transportziel zurücklegen. Die flexible und platzsparende Konfiguration erlaubt ein kundenspezifisches individuelles Anlagenlayout, inkl. der Integration von Pufferzonen, dem Transport über mehrere Etagen und unter der Decke. Zudem ist jederzeit eine Anpassung an geänderte Prozessabläufe sowie eine beliebige Systemerweiterung möglich. Darüber hinaus können auch die Shuttles in Länge und Breite individuell an die Bedürfnisse von Airbus bzw. die zu transportierenden Güter angepasst werden.
Das montrac-Transfersystem findet seinen Einsatz weltweit in Industriebetrieben – unter anderem bei vielen führenden Automobilherstellern. Vor allem bei der Fertigung von Scheinwerfern, Türen, Türschlössern oder Autositzen sind die erschütterungsfreien Hightech-Transportsysteme gefragt. Das künftige Wachstum soll vor allem durch Produktinnovationen und die verstärkte Internationalisierung des Geschäftsmodells generiert werden.