Distributionszentren : Aus diesem Hochregallager wird Schweden mit Möbeln versorgt
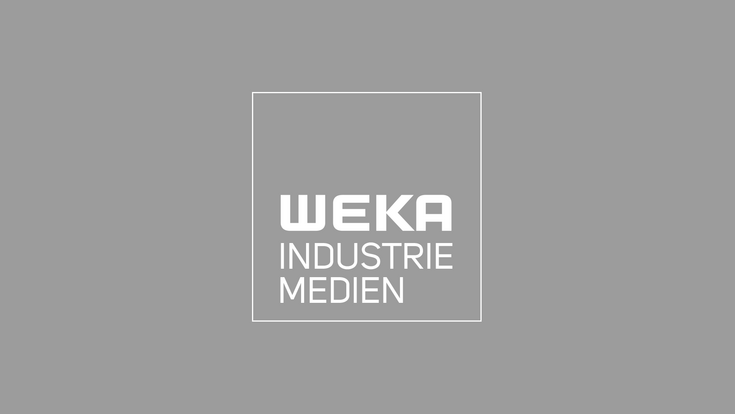
Spätestens, als das neunte externe Lager genutzt werden musste, fiel die Entscheidung für eine neue Logistiklösung. „Warentourismus“ nennt Jysk-Logistikmanagerin Annika Löfgren diese Fragmentierung und erklärt: „Mit der Kapazitätserweiterung wollten wir das beenden, die Warenlagerung an einem Standort konsolidieren und die Prozesse mit moderner IT und Fördertechnik weiter optimieren.“ Konkret ging es um die Einrichtung eines dritten Hochregallagers (HRL) und die Automation der bestehenden Anlage.
Dass Jysk schließlich SSI Schäfer an Bord holte, war nicht nur deren Konzept für die Erweiterung geschuldet – gemeinsame Großprojekte in Dänemark und Polen hatten bereits überzeugt, und daher war die Projektvergabe laut Löfgren „folgerichtig“: „Damit haben wir auch den Vorteil eines einheitlichen Systems in all unseren großen Lagern auf dem Kontinent.“ Der Auftrag erging Ende 2013, und bereits im Juli 2015 konnte der Möbelhändler mit der Auflösung der externen Lager und der Einlagerung in den 76.000 Stellplätzen des neuen, zehngassigen HRL in Nässjö beginnen. Das neue HRL dient als Nachschublager für die beiden vorhandenen HRL. Über einen Fördertechnik-Bypass können Auslagerungen zudem direkt an die Kommissionierplätze erfolgen.
Das Ergebnis der Zusammenarbeit ist eines der größten und modernsten Distributionslager Skandinaviens: mit mehr als 165.000 Palettenstellplätzen, durchgehend automatisierten Prozessen und einer leistungsstarken Logistiksoftware. Die Tagesleistung erreicht bis zu 1.100 Paletten im Wareneingang und 1.000 Paletten im Warenausgang. Hinzu kommt die Verarbeitung von etwa 6.000 Paletten für die Kommissionierung oder gesamter Paletten auf der Fördertechnik. Dank konsequenter Trennung der Materialflüsse und deutlich erhöhter Effizienz der Kommissionierprozesse ist der Standort Nässjö auf eventuelles Wachstum vorbereitet. Heute sind hier 5.200 verschiedene Artikel gelagert, insgesamt an die 14 Millionen Einzelteile. Das Distributionszentrum versorgt alle Jysk-Stores in Schweden und in Finnland.
Schrittweise Umsetzung
Die Umsetzung des Projekts erfolgte in mehreren Schritten: Während der Betrieb in der Bestandsanlage fortgeführt und die Arbeiten an dem neuen HRL aufgenommen wurden, wurde die direkt vor dem geplanten Neubau und bereits in einem früheren Bauabschnitt errichtete Lagerhalle zu einer reinen Wareneingangshalle mit neuer Fördertechnik und einem verbleibenden Flachlagerbereich für Sonderpaletten umgebaut. „In diesem Trakt des Logistikzentrums wurde eine Bühnenebene eingezogen, auf der ein Teil der Fördertechnik installiert ist, um Flächen für den Gabelstaplerverkehr auf der Bodenebene freizuhalten“, erzählt Anders Bohlin, Vertriebsmanager bei SSI Schäfer.
Parallel dazu entwickelte SSI Schäfer über Projektsimulationen ein Materialflusskonzept mit getrennten Wareneingangs- und Warenausgangsströmen. „Einerseits mussten die beiden HRL der Bestandsanlagen modernisiert und fördertechnisch optimal in ein umfassendes Materialflusskonzept eingebunden werden“, sagt Bohlin. „Andererseits galt es, eine Software aufzusetzen, die über alle Lagerbereiche hinweg eine koordinierte Prozesssteuerung ermöglicht.“ Jysk entschied sich für die Ablösung des Altsystems und die Implementierung der Logistiksoftware WAMAS von SSI Schäfer. „Das Standardsystem wurde exakt auf die Anforderungen von Jysk zugeschnitten und an das überlagernde SAP-System angebunden“, erzählt Anders Bohlin.
Hardware und Steuerung im Fokus
Dazu wurden in einem Retrofit-Projekt zunächst die Hardwarekomponenten der Bestandsanlagen auf den aktuellen Stand der Technik gebracht. Gerhard Wolf, Projektmanager von SSI Schäfer: „Die Steuerungen der Fördertechnik und Regalbediengeräte mussten ausgetauscht und die Fördertechnik teilweise ertüchtigt werden. Die Leistungsfähigkeit der beiden vorhandenen HRL sollte ermittelt und für ein optimales Zusammenspiel mit dem neuen HRL in die Prozesssteuerung von WAMAS eingepflegt werden.“
Zudem wurde die Steuerung der Fahrerlosen Transportfahrzeuge, die im Flachbau vor dem neuen HRL die innerbetrieblichen Transporte übernehmen, in das Lagerverwaltungssystem eingebunden. Damit übernimmt WAMAS die koordinierte Prozesssteuerung in allen vier Lagerbereichen des Distributionszentrums: den drei HRL-Komplexen nebst Fördertechnik sowie einem Flachlager in einer bestehenden Kommissionierhalle, aus dem die Kommissionierung von Großteilen erfolgt.
Internationalisierung treibt Komplexität
Als zusätzliche Herausforderung stellte sich die Internationalisierung der Warenströme dar: Die in Nässjö angelieferten Artikel kommen von verschiedenen Lieferanten in und auf unterschiedlichen Ladehilfsmitteln. Im Umlauf sind sowohl Euro- als auch Großpaletten mit Maßen bis zu 1.200 x 2.400 Millimeter. Insgesamt wird im Jysk-Distributionszentrum inzwischen mit sechs unterschiedlichen Paletten-, Käfig- und Plattformgrößen gearbeitet. „Die Kommissionier-Fördertechnik war ursprünglich jedoch nur für Europaletten ausgelegt“, erzählt Gerhard Wolf. „Da haben wir entsprechend den aktuellen Anforderungen nachgesteuert.“
Maßgeschneidertes Paletten-Handling
Konkret bedeutet das: Regalbau, Regalbediengeräte und Fördertechnik des neuen HRL-Komplexes sind durchgängig auf die größten Formate der Ladungsträger ausgelegt. Um auch die vorhandene (Kommissionier-)Fördertechnik weiterhin nutzen zu können, entwickelte SSI Schäfer spezielle Unterpaletten und installierte je eine Auf- und Absattelstation für die angelieferten Großpaletten. Sie sind in die Fördertechnik im Vorgebäude des neuen HRL integriert. Dabei werden die Unterpaletten in einem geschlossenen Kreislauf geführt: Die Unterpaletten aus der Absattelstation werden automatisch gestapelt und in Stapelspeichern mit bis zu sieben Zehnerstapeln vorgehalten. Bei Bedarf in der Aufsattelstation erfolgt eine automatisierte Entstapelung und entsprechende Zuführung. An der Aufsattelstation werden die angelieferten Großpaletten um etwa 20 cm angehoben und jeweils eine Trägerpalette darunter geschoben. „Die Sonderkonstruktion der Unterpaletten ermöglicht es, die Altförderstrecken auch für die großen Ladungsträger nutzen zu können“, erklärt Wolf. Verfahrwagen kommen im neuen HRL übrigens nicht zum Einsatz. SSI Schäfer setzte auf eine Lösung mit Eckumsetzern und Drehrollenbahnen.
1,2 Kilometer Fördertechnik
Die Lagerware wird an zehn Wareneingangstoren angeliefert. Für das automatisierte Handling der Ladungsträger sind vier Aufgabestationen eingerichtet, die von Hubwagen, Staplern und FTS bedient werden. An Ident-Punkten auf der Fördertechnik erfolgen die automatische Vereinnahmung, IT-Erfassung, Konturen- und Gewichtskontrolle, eine automatisierte Etikettierung sowie die Transportsicherung der Paletten durch automatische Folienwickler. Damit sind die Wareneingänge für den weiteren innerbetrieblichen Materialfluss präpariert – sofern WAMAS sie, wie etwa bei Schnelldrehern, nicht direkt in die Kommissionierhalle oder den Warenausgang aussteuert. Insgesamt sind sieben Konturenkontrollen in die Anlage integriert. „Wir sind auf ein optimiertes Lager bedacht und nutzen daher für die Auftragszusammenstellung sowohl das Cross Docking als auch die Kommissionierung gelagerter Artikel“, erzählt Jysk-Logistikmanagerin Annika Löfgren.
Die Fördertechnik führt die Wareneingangspaletten an einen von zwei Liften. Die Senkrechtförderer bringen die Paletten auf eine Transportbrücke und von dort über zwei weitere Lifte an die Übergabestationen ins neue HRL. Daran angebunden ist die Fördertechnik zu den beiden Bestandsanlagen und den Kommissionierplätzen. Inklusive der Verbindung von den Wareneingangstoren und zu den Warenausgangsbahnen umfasst die vorgelagerte Fördertechnik mit 189 Rollenbahnen und 325 Kettenförderern eine Gesamtlänge von 1,2 Kilometern.
Die redundante Verteilung der Wareneingangspaletten auf die zehn Gassen des neuen HRL steuert WAMAS über die nach Vorgabe des Lagerverwaltungssystems im Wareneingang erzeugten Materialflussetiketten. Die Einlagerung der Paletten mit Gewichten von 1.000 kg (Euro-Paletten) bis 1.500 kg (Plattformen) sowie Fachhöhen im neuen HRL von bis zu 2,80 m erfolgt chaotisch, doppeltief. Im neuen HRL sorgen zehn energieeffiziente Zweimast-Regalbediengeräte vom Typ Exyz für effiziente Ein- und Auslagerungsprozesse.
WAMAS versorgt Kommissionierplätze
Vollpaletten für den Warenausgang und zur Versorgung der Kommissionierplätze werden über separate Senkrechtförderer an die Kommissionier- und Bereitstellungsflächen auf der Flurebene unter der Fördertechnikbühne übergeben. An den Übergabeplätzen nehmen Stapler die Paletten ab und transportieren sie – geführt vom integrierten Staplerleitsystem – zu den von WAMAS vorgegebenen Abstellplätzen. Für die Nachschubversorgung der Kommissionierplätze aus dem neuen HRL stößt WAMAS auf Basis seiner Bestandsverwaltung die entsprechenden Prozesse an. Die Großladungsträger werden an die Aufsattelstation ausgelagert, auf Unterpaletten gesetzt und auf der Altfördertechnik in die Kommissionierbereiche geführt. Anbruchpaletten gelangen über die Absattelstation zurück in das neue HRL. Die Kommissionierplätze selbst hat SSI Schäfer mit einem Pick-by-Light-System modernisiert, das für eine sichere Auftragskommissionierung sorgt. Zur Arbeitserleichterung unterstützen 21 Scherenhubtische die ergonomisch optimierten Kommissionierprozesse.
Eigene Leerpaletten-Prüfbahn
Für das Leerpaletten-Handling wurde in Nässjö eigens eine Leerpaletten-Prüfbahn für Europaletten eingerichtet. Mit modernsten Druckrollen-Zug- und Sensorprüfungen werden die einlaufenden Paletten auf ihre Qualität und Belastungsfähigkeit geprüft. Je nach Untersuchungsergebnis separiert die Anlage die Paletten dann in hochregallagerfähige, noch für den Staplerbetrieb geeignete oder unbrauchbare Ladungsträger. Die HRL-fähigen Paletten werden gestapelt und auf Abruf automatisch in einem der drei HRL eingelagert.
Auftraggeber
Die dänische Jysk-Gruppe (in Österreich: „Dänisches Bettenlager“) wurde 1979 in Aarhus gegründet und verfügt heute über mehr als 2.500 Fachgeschäfte in 48 Ländern. Der Möbelhändler macht mit gut 21.000 Beschäftigten einen Jahresumsatz von knapp drei Milliarden Euro.
Auftragnehmer
Der Spezialist für modulare Lager- und Logistiksysteme SSI Schäfer Gruppe (Hauptsitz: Neunkirchen, D) beschäftigt weltweit in rund 70 operativ tätigen Gesellschaften und an zehn Produktionsstätten rund 10.000 Mitarbeiter. SSI Schäfer plant, konzeptioniert und produziert Systeme zur Einrichtung von Lagern, Betrieben, Werkstätten und Büros, manuelle und automatische Lager-, Förder-, Kommissionier- und Sortiersysteme sowie Lösungen für Abfalltechnik und Recycling. Außerdem bietet die Gruppe releasefähige Software für den innerbetrieblichen Materialfluss.
Diese Story finden Sie auch in dispo Ausgabe 3/2018.