Anwenderbericht Fördertechnik : HLF Heiss setzt Fördertechnik für Autostore bei Rexel um
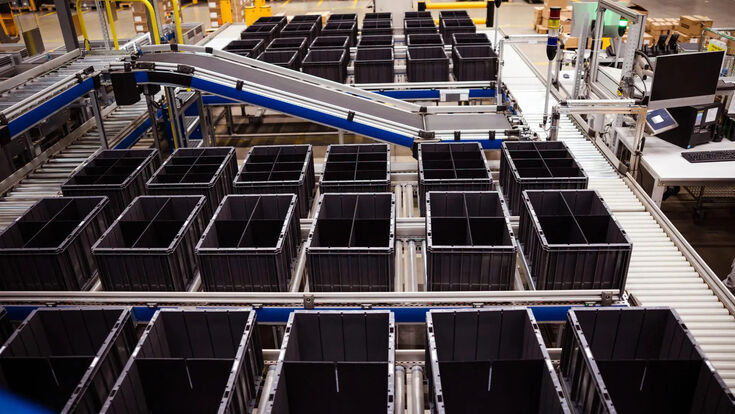
Rexel Austria investiert viel in moderne Logistik und hat dafür bereits vor einigen Jahren die Auszeichnung "Bestes Logistikzentrum Österreichs" erhalten. Das Hauptzentrallager in Weißkirchen an der Traun bildet seit über 15 Jahren das logistische Rückgrat des Unternehmens. Hier laufen die Fäden zusammen, um die bedarfsgerechte Servicierung sicherzustellen. Dabei verspricht Rexel 24-Stunden-Lieferung durchs ganze Land, meist sogar noch schneller. Mehr als 200 Mitarbeiter:innen aus über 23 Nationen wickeln im Logistikzentrum auf rund 23.000 m2 mehr als 20.000 Bestellpositionen täglich ab. Mehr als die Hälfte davon, Tendenz steigend, wird online bestellt.
Nun hat der Elektrogroßhändler seine Intralogistik mit einem Autostore im Zentrallager Weißkirchen weiter vorangetrieben - als Ergänzung musste auch eine effiziente Förderanlage her. Jetzt steuern an die 500 Laufmeter verbaute Fördertechnik von HLF Heiss den Materialfluss in die erforderlichen Funktionsbereiche.
Ziel von Rexel war es, durch die im Autostore umgesetzte Automatisierung die Ein- und Auslagervorgänge zu optimieren, die Effizienz zu steigern und damit die Wettbewerbsfähigkeit zu stärken. Die Förderanlage gliedert sich nun in zwei wesentliche Funktionsbereiche, nämlich zum einen in eine Behälterförderanlage für die Autostore Lagerbehälter, zum anderen in eine Förderanlage für Paket- bzw. Versandbehälter.
Bei den meisten Anwendungen werden die Einlagerungen direkt an den Ports bewerkstelligt. Bei Rexel Austria hat man einen anderen Weg gewählt. Das Fördersystem dient zum Transport der Autostore-Behälter aus dem und in das Autostore-Lager, für die zentral angeordnete Wareneinlagerung, diese befindet sich nahe des Wareneingangsbereiches.
Für die Lagerung werden ganze und unterteilte Behälter verwendet. Diese insgesamt vier Behältertypen werden auf Pufferbahnen an den Wareneingangsarbeitsplätzen bereitgestellt. Der Mitarbeiter befüllt den ausgewählten Autostore Behälter bzw. nur das passende Fach, nach einer automatischen Gewichts- und Höhenkontrolle wird der Behälter in das Autostore-Lager, an den Übergabeplatz für den Roboter, transportiert.
Von 16 Arbeitsplätzen, ausgeführt als Carousel Ports, verläuft über den Ports die Abtransportstrecke für die kommissionierten Aufträge entweder in einem passenden Karton oder in einem genormten Versandbehälter. Jeder Arbeitsplatz ist mit einem elektrisch höhenverstellbaren Packtisch mit der erforderlichen Ausstattung, wie Auszüge für Drucker, Bildschirmhalterung, Ablage für Tastatur und Maus, Kartonmagazin, Füllmaterialbehälter, persönliche Schublade, etc. ausgestattet. Eine elektromechanische Hubstation, welche zwischen Packtisch und Fördersystem positioniert ist, hebt schwere Packstücke vom Arbeitstischniveau von ca. 800 mm auf das Förderniveau von 1150 mm an.
Das zweite Fördersystem, die Versandförderanlage, dient dem Warentransport von den Kommissionierstationen des Autostore-Systems zu den Tourenbahnen für die Versandbereitstellung. Kleine Pakete, die als Briefsendungen gelten, laufen zu einem eigenen Sorter, wo nach Postleitzonen sortiert wird.
Nach dem automatischen Verwiegen und Umreifen werden die Versandeinheiten zu den Zielbahnen transportiert. Es gibt 13 Tourenbahnen für den Speditionsversand bzw. die Eigenauslieferung und neun weitere Ziele für den Postversand. Vor den Zielbahnen sitzt das Barcode-Identifikationssystem. Mittels OPC-Server geben wir die Versand ID an den Kundenrechner weiter, dieser gibt der Förderanlagensteuerung das jeweilige Ziel vor.
Die Versandeinheiten (Versandkartons, Versandbehälter und Kleinpakete) werden mittels Zahnriemenausschleusern dem richtigen Ziel zugeteilt. Die Kleinpakete werden direkt in eine Palettenbox abgeworfen.